Renewable Energy Workshop - Bio-Gas in Himachal - Part 1
As part of the ConservEN program, four of my intern colleagues and I recently participated in a two-day Biogas Workshop aiming to increase basic awareness of biogas plants and their potential as a renewable energy source in Northern India.
On the first day of our workshop, we learned how a biogas plant functions and why it may be a beneficial sustainable energy source for the communities we live in.
A biogas plant produces clean gas through the digestion of cow dung and non-woody biomass waste. The resulting biogas is used as a low-cost fuel for various energy needs. This workshop focused primarily on using biogas for cooking as an alternative to LPG (liquid petroleum gas), a limited environmental resource.
Biogas plants provide an extensive list of benefits. The input, most commonly cow dung mixed with water, has high levels of the greenhouse gas methane. After biogas digestion, however, the biogas plant emits the processed cow dung as waste with significantly lower levels of methane. This “waste” product can be used as a nitrogen rich, odorless organic fertilizer full of beneficial bacteria that’s easily absorbed by plants. Therefore, the biogas plant not only provides a sustainable source of cooking fuel, it also supports rural sanitation, organic plant growth, and greenhouse gas reduction.
The Indian Ministry of New and Renewable Energy provides subsidies for biogas plant construction, reducing the 30,000 rupee cost to roughly 20,000 rupees.
On the second day, we visited several working biogas plants in nearby villages. First, we visited the village of Charhi, where the head of the village, Mr. Dadwal, invited us into his home to study his biogas digester.
This biogas plant was built 20 years ago for a cost of approximately five thousand rupees (roughly 100 US dollars), which was quite an important amount at the time. The biogas plant features an aboveground input tank to insert the dung mixture, connected to the underground concrete reservoir where anaerobic process occurs and produces the gas. The waste outlet expels the processed dung as pressure builds. They feed the biogas plant roughly five kg of cow dung each day from their one cow, producing two-three hours of biogas cooking fuel daily. The family uses up to two cylinders of biogas per month due to the reception of many guests, which is linked to the position as head of the village of the father.
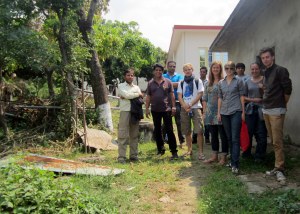
The Biogas Workshop participants. From left to right in foreground: Gulshan (cultural liaison officer, far left), interns- Clement, Aureline, Katrina, Mandy and Adrien
The second visit took us to Mr. and Mrs. Shamsher’s home, near the EduCARE intern house in Maiti. Like Mr. Dadwal’s family, this family has an important role in the community as current village committee members.
Mrs. Shamsher kindly demonstrated how to use their 18-year-old biogas plant, a similar model to the plant in Charhi.
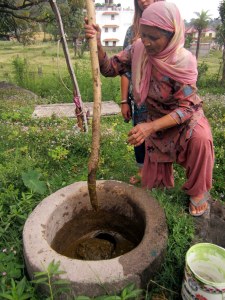
Then, she mixed the dung and water together and removed the stone that allows the mixture to enter the reservoir where anaerobic digestion occurs.
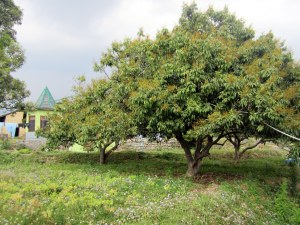
On the top of the concrete biogas reservoir, she opened a valve that released the gas into the gas line. Here you can see the gas line carried through the trees to their kitchen.
She also welcomed us into her kitchen where she uses three sources of energy for cooking: wood, biogas and LPG. According to her experience, the biogas flame is slightly weaker compared to the LPG and provides the slower heat best suited for cooking chapatti bread and vegetables. She uses the biogas for 75% of their cooking, up to 2-3 hours per day, with dung supplied from their three cows. One supplemental cylinder of LPG now lasts her 3-4 months. During the winter, she uses the stove more often because of the heat it provides to her home.
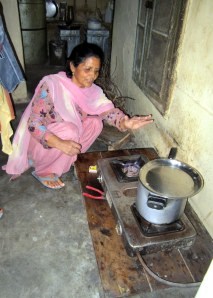
Her three energy sources for cooking (biogas, wood stove, and LPG) increases her self-reliance if biogas supply is low.
After visiting these two biogas digesters, we visited Mr. Ramesh’s Nirmayam Trust Organic Farm close to Maiti.
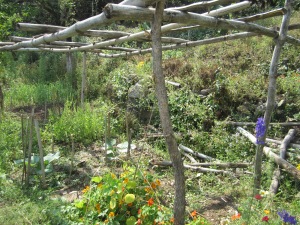
The farm applies organic farming, permaculture, and natural farming principles by growing several kinds of plants in the same area. This creates resistance to pests by increasing biodiversity.
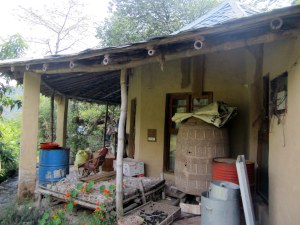
Natural building made of stone and clay plaster with a roof made of slate rock. Although concrete is becoming more popular, this style of natural building is still common in the local villages.
The farm holds up to ten cattle in the barn, but they aren’t currently processing the dung for energy use. This is a good example of the biogas plant potential in the area as biomass/dung is readily available.
Finally, we visited Dr. Anjan Kumar Kalia in Dharamshala at his renewable energy shop and information center. As a retired professor of Palampur Agricultural University, Dr. Kalia is a leading expert in biogas processes in India and has travelled extensively around the world to present his works in several environmental conferences.
He provided us with valuable, relevant information from his research on the current biogas use in India.
His statistical highlights focus on the state of Himachal Pradesh, where half of the ConservEN and EduCARE interns currently work:
- Cattle to human ratio = nearly 1:1
- Dung from these cows could fuel 319,482 biogas plants
- 319,482 biogas plants = domestic energy needs of 1.24 million people
- 45,000 biogas plants currently installed = only 14% of potential
- Carbon credit can be sold by rural villagers with biogas plants to the International Carbon Market for reducing methane gas production
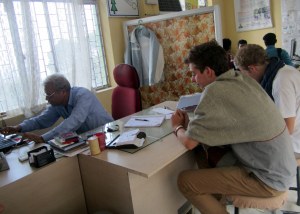
Dr. Kalia also provided us with advice and guidance on how to fix the issues Adrien encountered with his ambitious homemade biogas plant.
After two days of workshop training, we gained a deeper awareness of biogas production. Most importantly, we began to process and discuss the potential of biogas usage in the communities around our centers in Himachal Pradesh and Punjab.
Next, we plan to develop Adrien’s model of a biogas plant and gather additional knowledge on our communities’ need and interest in relation to biogas use. We’re excited to share our experience and knowledge at our REstore office, to open in the next month or two.
by Adrien Calvez Petit (France) and Katrina Sill (US)
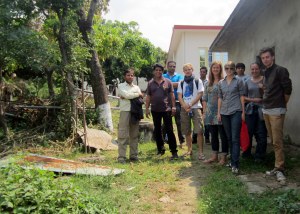
The Biogas Workshop participants. From left to right in foreground: Gulshan (cultural liaison officer, far left), interns- Clement, Aureline, Katrina, Mandy and Adrien
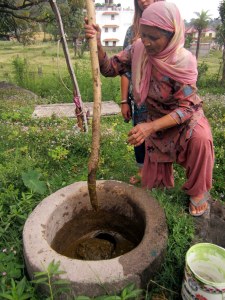
Then, she mixed the dung and water together and removed the stone that allows the mixture to enter the reservoir where anaerobic digestion occurs.
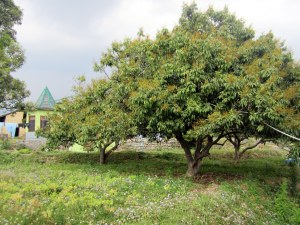
On the top of the concrete biogas reservoir, she opened a valve that released the gas into the gas line. Here you can see the gas line carried through the trees to their kitchen.
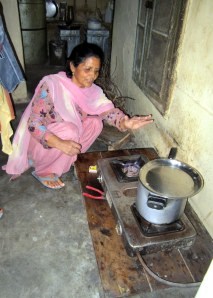
Her three energy sources for cooking (biogas, wood stove, and LPG) increases her self-reliance if biogas supply is low.
After visiting these two biogas digesters, we visited Mr. Ramesh’s Nirmayam Trust Organic Farm close to Maiti.
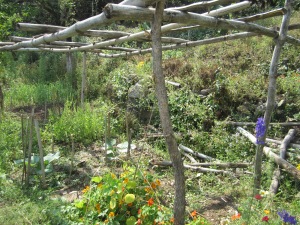
The farm applies organic farming, permaculture, and natural farming principles by growing several kinds of plants in the same area. This creates resistance to pests by increasing biodiversity.
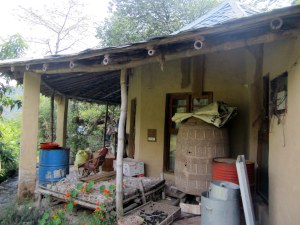
Natural building made of stone and clay plaster with a roof made of slate rock. Although concrete is becoming more popular, this style of natural building is still common in the local villages.
The farm holds up to ten cattle in the barn, but they aren’t currently processing the dung for energy use. This is a good example of the biogas plant potential in the area as biomass/dung is readily available.
Finally, we visited Dr. Anjan Kumar Kalia in Dharamshala at his renewable energy shop and information center. As a retired professor of Palampur Agricultural University, Dr. Kalia is a leading expert in biogas processes in India and has travelled extensively around the world to present his works in several environmental conferences.
He provided us with valuable, relevant information from his research on the current biogas use in India.
His statistical highlights focus on the state of Himachal Pradesh, where half of the ConservEN and EduCARE interns currently work:
- Cattle to human ratio = nearly 1:1
- Dung from these cows could fuel 319,482 biogas plants
- 319,482 biogas plants = domestic energy needs of 1.24 million people
- 45,000 biogas plants currently installed = only 14% of potential
- Carbon credit can be sold by rural villagers with biogas plants to the International Carbon Market for reducing methane gas production
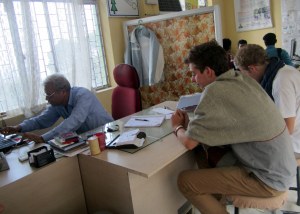
Dr. Kalia also provided us with advice and guidance on how to fix the issues Adrien encountered with his ambitious homemade biogas plant.
After two days of workshop training, we gained a deeper awareness of biogas production. Most importantly, we began to process and discuss the potential of biogas usage in the communities around our centers in Himachal Pradesh and Punjab.
Next, we plan to develop Adrien’s model of a biogas plant and gather additional knowledge on our communities’ need and interest in relation to biogas use. We’re excited to share our experience and knowledge at our REstore office, to open in the next month or two.
Renewable Energy Workshop - Biomass in Punjab - Part 2
Recently, the interns involved in the Biogas Workshop held in Himachal Pradesh were treated to an extra day of field visits related to renewable energy in Punjab. The biomass plant visit was among the many highlights of this extended workshop.
Located near Nakodar, the Green Planet Energy Ltd Biomass Plant produces 7,000 kilowatts of energy per hour (KWh). Assuming the average house utilizes 3 KWh, this one plant produces enough energy to power 2,333 homes every hour. All of this energy is produced through the burning of biomass (organic) waste that would otherwise be burned in farm fields.
Benefits of the Biomass Plant:
- Alternative to burning biomass in fields, causing air pollution
- Saves habitat and ground cover
- Produces renewable energy – 2 KG biomass = 1 KW energy
- Gives extra income to farmers – 1 rupee = KG of hay or biomass
Biogas Plant Process:
- Farmers sell biomass waste to the plant
- Biomass is dried and compacted
- Compacted biomass is loaded onto the belt, leading to the furnace (see Photo 2)
- Biomass is used as fuel in boiler, reaching temperatures of 700 degrees Celsius
- Boiler heats 30 tons of water each hour (of which 2 tons evaporates, 28 tons reused)
- The boiling water creates steam
- Steam runs the turbine at 7500 revolutions per minute (RPM)
- Turbine produces electricity/power by running the generator
Waste Products/Emissions from Biomass Plant Processes:
Of course, burning the biomass fuel creates waste fumes. The fumes contain particles of carbon monoxide, a poisonous gas for humans to breathe, and carbon dioxide, a greenhouse gas widely considered to be contributing to global warming.
The workshop team in front of the electric static precipitator (from left to right: Clement, Adrien, Owen, Gulshan, Biomass Plant Engineers, Ariel, Katrina, Mandy, and Sevil)